Kaeser Csd 80 Compressors Manual
Keep the service manual in a safe place throughout the life of the machine. Request the supply of any missing documents from KAESER. 80 psig Pressure switch. Kaeser Compressors, Inc. Datasheets for Air Compressors. Fixed Speed Oil-free Screw Compressors -- CSG 90-2 / CSD 90-2 T / CGS 90-2 RD. Capacities: 106 to 1074 cfm Standard pressures: 80 to 217 psig The ASD T to DSD T series. Kaeser asd bsd and csd series 25 125 hp capacities from 106 to 576 cfm pressures from 80 to 217 psig screw compressors.
Kaeser Csd 80 Compressor Manual
. SERVICE MANUAL Screw Compressor Model: CSD 75 GL-Nr.: 10-00 01.Volt Cabinet heaters Wye-Delta Start 115 V receptacle D.O.L. Table of Contents Chapter - Page Technical Specification. 1 - 1 Compressor Unit. Table of Contents Chapter - Page Putting into Operation.
7 - 22 Points to be Observed before Putting into Operation. Table of Contents Chapter - Page 11 Appendix.11 - 53 11.1 Wiring Diagram. CSD 75 Maximum gauge working pressure. Installation Requirements Max.
Height above sea level of the place of installation 3000 ft. (for all heights above please contact authorized KAESER distributor) 40 EF Min. Ambient temperature.
M - SERIES SEMI - SYNTHETIC LUBRICANTS M-Series SIGMA compressor fluids are the highest quality petroleum lubricants. M-460 is specially blended to provide reliable performance in KAESER screw com- pressors.
S- SERIES SYNTHETIC LUBRICANTS S-Series SIGMA compressor oils are formulated from the most advanced synthetic lubricants. 9.12 proper draining procedure.
Compatibility of KAESER Sigma Lubricants All the above listed KAESER Sigma lubricants are similar to mineral oil in their compatibility with paints, seals, gaskets and hoses. The typical precautions are required when changing over from mineral oil to KAESER synthetic hydrocarbon based lubricant. Technical Specification ACCEPTABLE NOT RECOMMENDED Viton Celcon High Nitrile Buna N Neoprene Teflon SBR Rubber Epoxy Paint Low Nitrile Buna N Oil Resistant Alkyd Acrylic Paint Nylon Lacquer Delrin Polystyrene Attention! Polycarbonate bowls can be etched by any synthetic lubricant. We recommend replacement with metal bowls, or the addition of metal guards. Technical Specification 1 - 6.
Safety Safety Regulations Read this service manual carefully and observe cautionary references before putting this compressor package into operation and before carrying out any maintenance. Explanation of Symbols and References This symbol is placed before all references to safety where danger to life and limb can occur during work. These recommendations do not supersede other applicable codes.
Spare Parts Safe and reliable operation of the compressor package is guaranteed only with KAESER original spare parts and KAESER SIGMA cooling oil. Compressed Air System If a compressed air system is extended or changed, verify that the blowoff pressure and capacities of the safety relief valves on the air receiver tanks and in the system match the rating of all the compressor packages installed.
Safety Environmental Protection Condensate drainage The condensate accumulating during compression must be fed via a suitable drainage system, collected in special canisters and disposed of according to environmental regulations. Maintenance materials/wear items/replacement parts Ensure that all wear items, maintenance and replacement parts accu- mulating during operation of the compressor package are disposed of according to environmental regulations. Copyright KAESER COMPRESSORS, INC. All rights reserved. No part of this manual may be reproduced in any form without per- mission of KAESER COMPRESSORS, INC. Transport Transport Transport Instructions We recommend a fork lift truck or lifting equipment for transporting the compressor pack- age to avoid damage to the cabinet and framework. 35” Measurements in inches Spreader bar Do not exert any side forces on the compressor package when trans- Attention!
Porting with lifting equipment!. Construction and Operation Construction and Operation Principle of Compression The stationary compressor package is fitted with a single stage, oil-injected airend. The two rotors, the driven male rotor and the female rotor, both mounted in antifriction bear- ings, are fitted into the airend. As the rotors rotate, air is drawn into the upper side through the inlet port and is compressed on the lower side. Construction and Operation Identification of the Components Position details in ( ) correspond with the Pipe and Instrument Flow Diagram (P & I Diagram) 1 Inlet valve (2) Control cabinet 2 Coupling (53) Oil separator tank 3 Drive motor (3) Air filter (1) 4 Oil filter (10) Oil/air aftercooler (11/13). Construction and Operation 5 - 14.
Construction and Operation 5 - 15. Construction and Operation DUAL Control Full load Idle Standstill Time In DUAL Control (combined idle and start -stop) the compressor normally runs at full - load, idle or standstill. The controller regulates the compressor package between full - load and idle. If the compressor package runs in idle for longer than the preset period (1) to (2), for example t = 6 min, the drive motor is stopped completely (2). Construction and Operation QUADRO Control p min Full load Idle Standstill Time rise decay Running period Idle/ standstill period Run -on period Stop point for the running period or idle / standstill period upper switching point lower switching point pressure rise time (the time during which the air system pressure rises rise from the lower to the upper switching point) pressure decay time (the time during which the air system pressure decays. Construction and Operation If the air systems pressure rises to the upper switching point and the running period has already expired, the compressor package is switched off after the run -on period has expired (2).
If the air systems pressure rises to the upper switching point before the running period has expired then the pressure decay time of the previous switching cycle is taken as the criterium for the selection of the operating mode: - If the pressure decay time t. Installation Installation Installation Requirements Attention! The compressor should be mounted on level surface. For any special application please consult with the manufacturer.
Safe operation of the compressor package is only ensured if the ambient temperature re- mains within the limits stated in chapter 1.6). If the compressor is used in the open, take care that it is protected against the direct rays of the sun and against the ingress of dust and rain.
Installation Solution B: Exhaust Air used for Space Heating The hot air is forced through a conduit (see chapter 1.6) into the room to be heated. Consult the manufacturer with regard to length of conduit and for maximum allowable pressure drop for this compressor package. Safe operation of the compressor package is guaranteed only if the temperature limits (see chapter 1.6) of the cooling air are adhered to.
Installation 1.25 x FLA wire correction factor (see chapter 1.4) temperature rating for 40C 100A 60C 0.82 100A 75C 0.88 6 - 21. Initial Start Putting into Operation Points to be Observed before Putting into Operation Every compressor package is given a test run at the factory and carefully inspected before shipment. The test run confirms that the package conforms to the specification data and runs perfectly. Initial Start During installation of the compressor unit, ensure that a distance of at least 40 ” is kept between the air intake of the unit and any wall. Check the oil level in the oil separator tank (see chapter 9.11). Check that the airend rotates in the correct direction (see chapter 7.4).
Initial Start Checklist Is the floor at the place of installation solid and level? yes no Is the space large enough for the compressor package or its components?
yes no Are inlet and exhaust air apertures available in sufficient size and number? yes no Are all components of the compressor package easily accessible?. Initial Start Direction of Rotation Check Attention! The compressor is wired for connection to a clockwise phase se- quence power supply.
A check of the direction of rotation can be made by testing the phase sequence. Arrows showing the direction of rotation are located on the motor and on the airend hous- ing. Initial Start Motor Overload Protection Switch Adjustment Before any adjustments are carried out to the compressor package, lock the main disconnect in the ”off” position in accordance with appli- cable lock out/tag out procedures (example: OSHA CFR 29 § 1910.147) to ensure the compressor does not restart. Initial Start Measures to be taken before Initial Start Follow the procedure detailed bellow before initial start, after an oil change or if the com- pressor has not been operated for a period of three months or longer before starting the compressor: 7.8.1 Pour a small quantity of oil into the air inlet port.
Operation Operation Control Panel 1 SIGMA CONTROL 2 EMERGENCY STOP pushbutton SIGMA controller The SIGMA controller (1) is fitted in the control cabinet in the compressor package and serves as the control panel. It has 11 keys and 9 LEDs. Operation of the compressor pack- age is determined by the settings programmed into the controller.
Operation 8.3.1 Function keys 1 ON key (“I”) Menu scroll - DOWN key 2 OFF key (“0”) Menu scroll - UP key 3 Timer ON/OFF key Escape key 4 Remote ON key Return key 5 Load/idle key Info - event key Acknowledge (reset) key 8.3.2 Light emitting diodes and plain text display. Operation Starting and Stopping the Compressor Unit Attention!
Do not start and stop the compressor package with the main discon- nect switch. The compressor must always be switched ON and OFF with keys (1) and (2).
To turn the compressor ON (local): Switch on the main disconnect switch. Operation Acknowledgement of Service Messages When maintenance is due the yellow LED (15) on SIGMA CONTROL flashes. Before any maintenance is due an initial warning is displayed to allow coordination of service and maintenance personnel and provision of necessary servicing materials. (lubricants, spare parts, etc.). Maintenance due is shown in the display (12).
Maintenance Maintenance Observe the following rules during all maintenance and servicing work: Work on power driven equipment may only be carried out by trained or specialized personnel. Follow all applicable OSHA and local safety regulations. If a power failure occurs, the compressor package starts again auto- matically (normal setting) provided the line pressure is lower than the pressure threshold parameter entered in SIGMA CONTROL. Maintenance Location of maintenance doors and cover panels 9 - 33. 3 years at the latest Annually Check all electrical connections for tightness and tighten if necessary Have the safety relief valve checked by authorized KAESER distributor Every two years Change the air filter. 0 h or after Remove motor bearing covers and/or end.
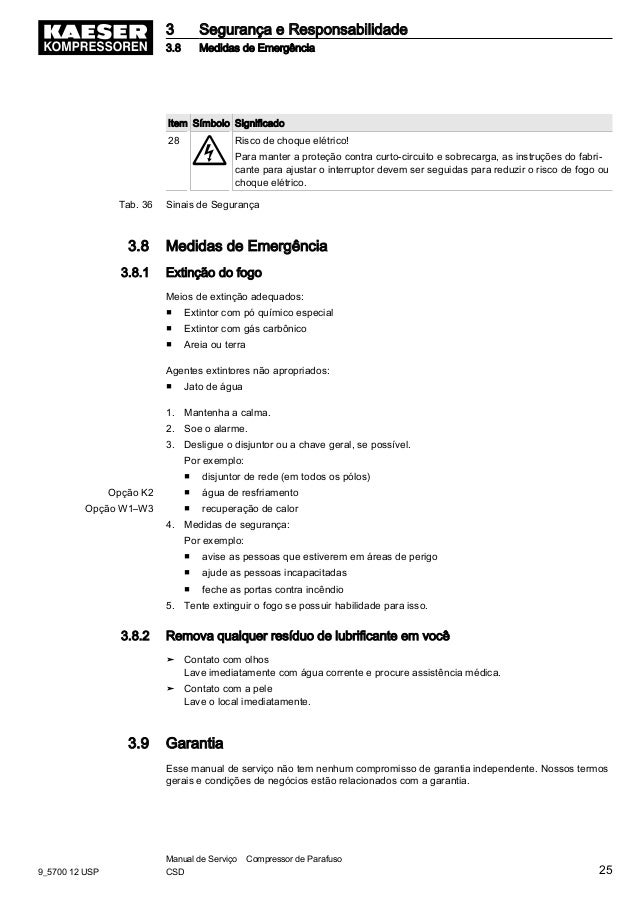
Do not use any sharp cleaning instrument that may damage the cooler. If the coolers are badly contaminated have them cleaned by authorized Attention!
KAESER distributor. 1 Air cooler 2 Oil cooler 3 Oil filter 4 Shut -off valve. Maintenance Cleaning or Replacing the Filter Mat Clean the filter mat every week depending on the dust content of the intake air and replace if necessary as detailed in the maintenance schedule (see chapter 9.3). Switch off the compressor package (see chapter 8.4).
Lock the main disconnect switch in the ”off”. Maintenance Remove cover panel (3, siee chapter 9.2). To open the air filter housing: Open the snap fasteners (1) on the dust collector (3) and remove the dust collector (3) with the insert. Take the insert out of the dust collector (3). Pull out the air filter cartridge (4) by turning slightly.
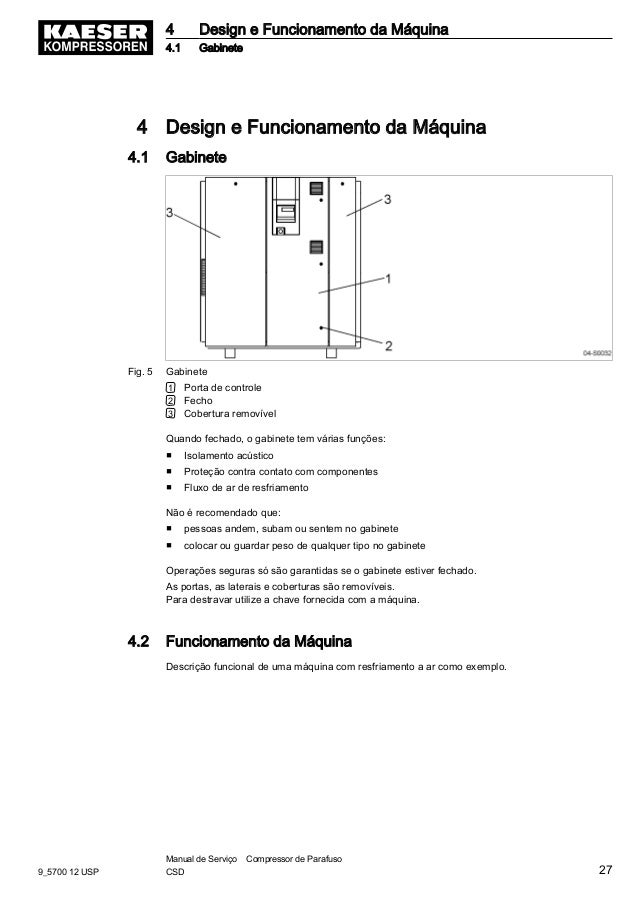
SIGMA CONTROL. See chapter 1.5 for the safety relief valve activating pressure. Have the safety relief valve tested by an authorized KAESER distribu- Attention! Tor in accordance with the maintenance schedule (see chapter 9.3).
Maintenance Venting the compressor unit Switch off the compressor unit (see chapter 8.4). Lock the main disconnect in the ”off” position in accordance with ap- plicable lock out/tag out procedures to ensure the compressor does not restart. Lock the isolation shut- off valve in the ”closed” position and vent all compressed air trapped between the compressor and the isolation shut- off valve in accordance with applicable lock out/ tag out pro- cedures. Maintenance Oil mist can escape when the oil separator tank is vented.
When inserting the maintenance hose into the compressor’s hose couplings, always have the ball valve closed and the hose end se- cured before slowly opening the ball valve. Beware of air/oil mist that could blow out of the hose. Maintenance Remove cover panel (2, siee chapter 9.2). 1 Oil filter cartridge 2 Turn in this direction to unscrew the cartridge Twist the used or contaminated oil filter cartridge counter clockwise to remove and catch escaping oil in a suitable container. Dispose of the old oil filter and any used, accumulated oil according to environmental care regulations! Clean the face of the combination block with a lint free cloth.
Maintenance 9.11 Topping off the oil The oil level indicator (9) of machines in operation should be checked weekly. The machine should be topped off with oil as soon as the minimum level (1) (border of green and red) is reached. Maintenance 1 Ball valve 4 Filler plug 8 Maintenance hose (6 -8) A shut (oil top - off) 9 Oil level indicator B open 5 Oil separator tank 10 Hose coupling 2 Pressure gauge 6 Nozzle 11 Ball valve (oil drain) 3 Hose coupling 7 Ball valve 12 Hose coupling. Maintenance Attention! Always use the same brand and type of oil when topping off the oil. (see label on the oil separator tank). During an oil change, drain the old oil completely and always replace the oil filter.
Never mix different oil types or brands. Oil recommendations see chapter 1.8 9.12 Oil Change (Oil Separator Tank and Oil Cooler). Maintenance 1 Ball valve 4 Filler plug 8 Maintenance hose (6 -8) A shut (oil top - off) 9 Oil level indicator B open 5 Oil separator tank 10 Hose coupling 2 Pressure gauge 6 Nozzle 11 Ball valve (oil drain) 3 Hose coupling 7 Ball valve 12 Hose coupling.
Maintenance Hang the maintenance hose into the container and secure. Open the oil drain valve (11).
Slowly open the ball valve (7). The remaining pressure in the oil circulation forces out the oil. When air escapes, close the ball valve (7) immediately. Close the oil drain valve (11). Maintenance 9.12.3 Draining the oil using own compressed air Shut down the compressor unit under full load (see chapter 8.4). Lock the main disconnect in the ”off” position in accordance with ap- plicable lock out/tag out procedures to ensure the compressor does not restart.
Maintenance Perform a test run When the operating temperature is reached (see chapter 1.1), shut down the compressor package (see chapter 8.4) and lock the main disconnect in the ”off” position in accordance with applicable lock out/ tag out procedures (example: OSHA CFR 29 § 1910.147) to ensure the compressor does not restart. Maintenance 14 Cover 16 Air pipe 20 Union nut 15 Dirt trap 17 Hexagonal screw 21 Gasket (with copper pipe) 19 Self -locking nut 23 Oil separator cartridge 25 Minimum pressure/check valve Remove cover panel (3, siee chapter 9.2). Loosen the union nuts (20) and lay the parts with connections carefully to the side - pull out the copper pipe at position (15). Maintenance Perform a test run When the operating temperature is reached (see chapter 1.1), shut down the compressor package (see chapter 8.4) and lock the main disconnect in the ”off” position in accordance with applicable lock out/ tag out procedures (example: OSHA CFR 29 § 1910.147) to ensure the compressor does not restart. Maintenance 9.14 Maintenance Schedule Model No. Serial No.Date Description of work Operating hours.
10.2 Service and Maintenance Agreement We recommend that you take out a service and maintenance agreement with an author- ized KAESER distributor. This is your best guarantee of reliable air supplies. Appendix Appendix 11.1 Wiring Diagram 11 - 53. Appendix 11.2 Maintenance Schedule Model No.
Serial No.Date Description of work Operating hours. Cooling air supply is inadequate. Provide required amount of ventilation. If cooling air outlet duct is used it may Consult authorized KAESER distributor be too narrow or too long. For duct requirements.
On air cooled units the fins of the cool. Appendix Possible cause: Remedy: Motor is running two phase: defective Check input power, check wiring, tigh- motor or blown fuse. Ten any loose connections. Replace fuse(s) or motor if necessary. Oil separator cartridge is contamina- Check pressure differential across car- ted. Full - load/Idle sequence occurs too frequently (short cycles) Possible cause: Remedy: Receiver tank size is too small or there Consult authorized KAESER distributor is no tank. For recommended tank size.
Diameter of hose connecting the unit Connecting hose diameter should not to the receiver tank is too small. Possible cause: Remedy: Wrong oil is being used in the unit.
Replace with correct oil type. Consult authorized KAESER distributor for other oil types not listed.
Oil separator cartridge has ruptured. Check pressure differential and re- place oil separator cartridge if neces- sary.
Rotary screw air compressor with direct drive 25-125 hp Compressor Specifications Models: ASD to CSD series Horsepower: 25-125 hp Capacities: 110-576 cfm Standard pressures 80-217 psig Maximum efficiency and reliability have long been synonymous with Kaeser Compressors. Our commitment to excellence drives us to continually enhance and optimize our compressed air system solutions. With a cutting edge research and development team committed to producing industry leading products, Kaeser constantly strives to offer lasting solutions for our customers' compressed air needs. The ASD - CSD series rotary screw air compressor delivers on all accounts. Rotary Screw Air Compressors with Direct Drive: Specifications Series Rated Motor Power Flow Capacity at 125 psig ASD 25 / ASD 30 / ASD 40S / ASD 40 25 hp to 40 hp 112 cfm to 191 cfm BSD 40 / BSD 50 / BSD 60 40 hp to 60 hp 193 cfm to 288 cfm CSD 60 / CSD 75 / CSD 100S / CSD 100 / CSD 125 60 hp to 125 hp 290 cfm to 565 cfm Integral Moisture Separator A moisture separator is integrated into the stainless steel discharge piping. This unique design maximizes separation with minimal pressure loss.
A zero loss Eco-Drain is standard to automatically remove the captured moisture. Electronic Thermal Management System The innovative Electronic Thermal Management system dynamically regulates fluid temperature to avoid internal condensation build-up, eliminating a common cause of lubricant degradation. Heat Recovery Ready Compressing air converts the electrical energy you pay for into heat. The ASD to CSD series are available with a option to easily recover up to 76% of this energy. You can harness additional heat recovery by ducting exhaust air.
In all, 9% of input energy is recovered as heat. The ASD series can come ready to be connected to an internal plate-type heat exchanger; The BSD and CSD series can be connected to an external heat exchanger or they can come with internal stainless steel plate type heat exchangers. Request Literature (Click on PDF icon to download electronically, or fill out the form below to receive a hard copy) ASD, BSD, CSD Series 25 to 125 hp, direct drive USASDBSDCSD DSD, ESD and FSD Series 125-450 hp, direct drive USDSD-FSD. First name.
Last name Your delivery address. Company. Street. City. State. Zip. Phone number.
E-Mail. What type of industry do you work in?
Most Viewed Pages
- Haynes Manual For 2015 Chevrolet Impala
- Kinetico Water Softener Installation Manual
- Zettili Solutions Manual
- Itil 2016 Study Guide
- Commercial Refrigeration Study Guide
- Volvo Marine Transmission Repair Manual
- Audi A6 2 7t Service Manual
- Treasures Workbook Teacher Manual
- Arnold Schwarzenegger Guide To Modern Bodybuilding
- Suzuki Service Manual 04 Ltz400
- Mazda E Series Service Manual
- Tire Condition Guide
- Padis Implementation Guide
- Vicon Spreader Parts Manual
- Study Guide For Epidemiology And Biostatistics
- 2000 Mercury 40 Elpto Manual
- 2016 Harley Road King Owners Manual
- 2016 Volvo S60 T5 Owners Manual
- 2007 Corolla Repair Manual